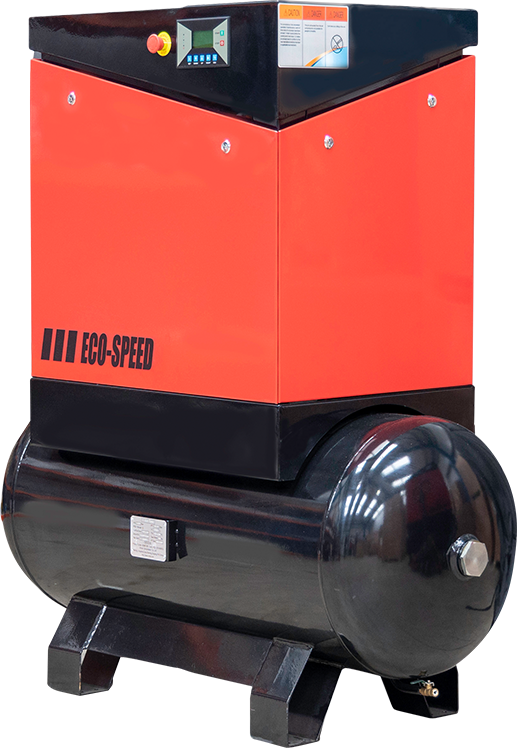
eco-speed
Fixed Speed Compressor
5.5 - 15 kw
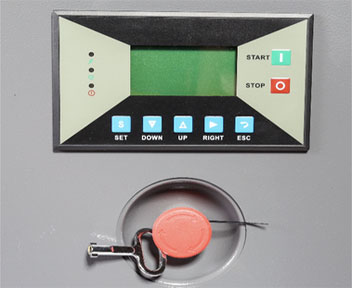
Digital Control Board
The AirWave Eco-Speed digital controller allows the user to change many useful parameters. The controller benefits from advanced monitoring and maintenance alarms too.
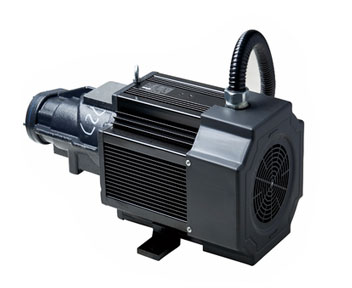
Direct Drive Motor
The electric motor is directly coupled to the compressor air end, for a true direct drive compressor. Low component count means less maintenance is required.
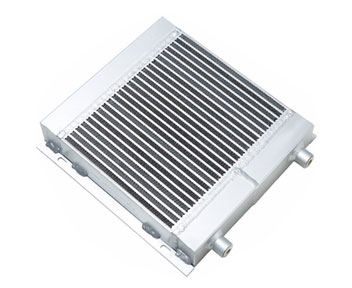
Large Capacity Cooler
High efficiency aluminium air/oil cooler guarantees optimum perfornamce in most environments.
Fixed Speed AM Series
USER FRIENDLY DESIGN
- USER FRIENDLY DESIGN
Silent and low vibration, user friendly design, optimized structure, low maintenance cost.
- PRODUCT HIGHLIGHTS
- The motor’s aluminum enclosure has high thermal conductivity which leads to good heat dissipation from the motor, low operating temperature, and long lifetime.
- Water, moisture, and dust resistant design ensures usability even in harsh environment.
- High precision processing guarantees the concentricity of the stator and rotor, uniform and consistent air gap, and stable operation. Simple yet good looking, practically designed for easy dismantling and reassembling.
- All Airwave compressors can be upgraded to include a Refrigerated Dryer with pre and oil removal filtration as standard
- HIGH COOLING EFFICIENCY
- TRUE DIRECT DRIVE
- LOW ENERGY LOSS
- Totally enclosed, silent, and anti-vibration design
- Durable filtration components
- Unique self-developed motor
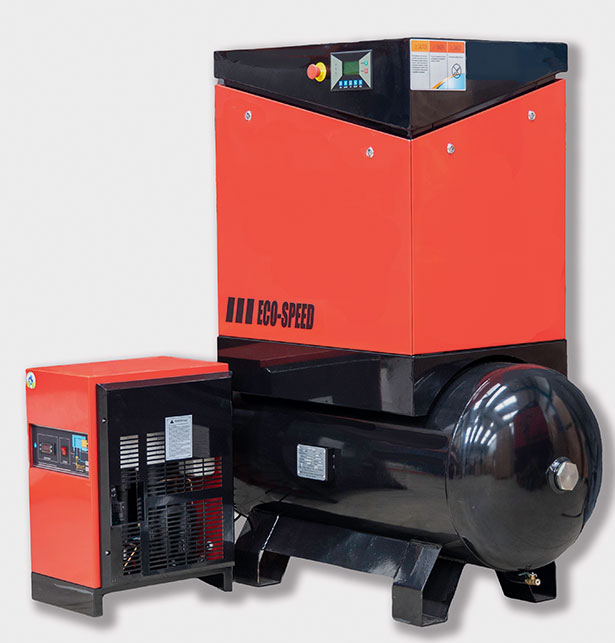
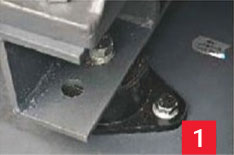
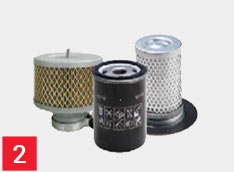
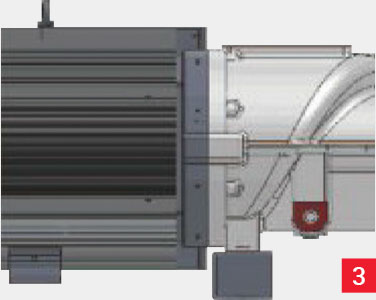
Technical Specification
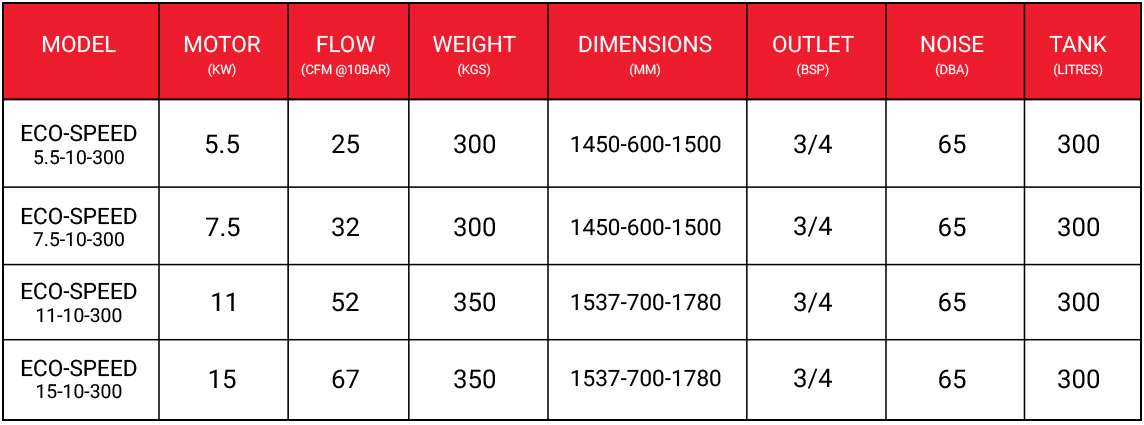
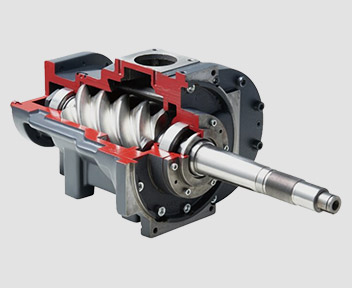
Airwave compressors unique Air-End design increases efficiency and working lifetime.
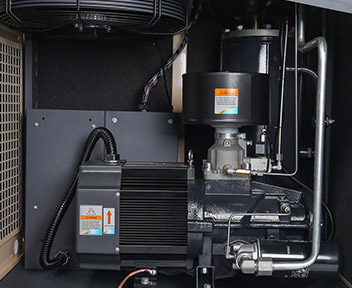
Full access to all major components which makes it very user friendly for maintenance
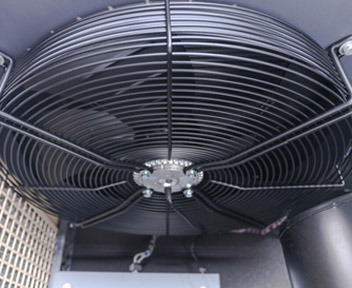
Large cooling capacity allows for optimum performance in many enviroments
Rotary Screw Compressor Air End
The heart of an air compressor is the screw pump which is also called air-end. The air-end is the most important part of any screw compressor. It’s that part of the machine where the actual compression takes place.
Why are they so popular? Since it’s a continuous process (as opposed to reciprocating piston compressors) they supply a steady, non-pulsating air flow, with minimum vibrations and maintenance and maximum lifetime.
How does an air-end work? Inside the compressor element are two screws that turn in opposite directions. The rotary screw compressor is a “positive displacement” compressor, which means that the air is physically squeezed together by an external force (like piston and scroll compressors).
In the case of the rotary screw, the air gets trapped between the two rotors. The rotors have a special design for optimal efficiency and performance. One rotor is the “male” and the other is the “female”. The air gets sucked in on one side (cold, low-pressure), and gets trapped between the rotors, and then is discharged out the other side (hot, high pressure).
This compression requires power, which is usually supplied by a electric motor, with the Airwave range of compressors, the airend is powered by the direct drive permanent magnet motor. The unique design of our airend incorporates the electric motor rotor shaft onto the male screw, which increases efficiency and reduces moving components extending its working life.
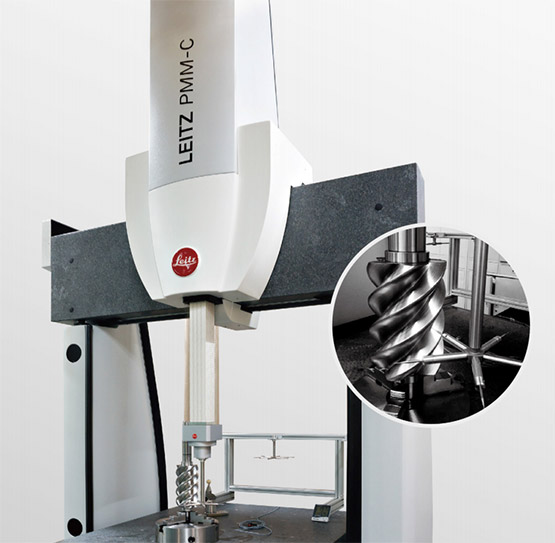
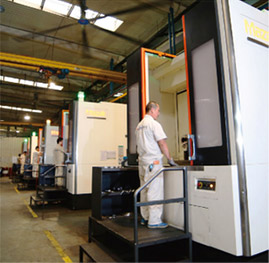
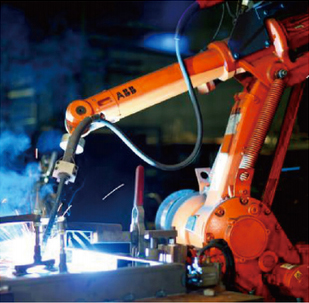
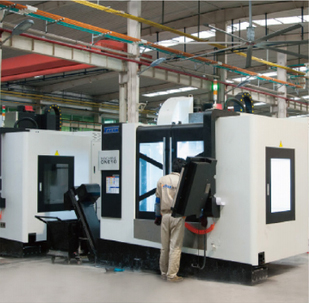
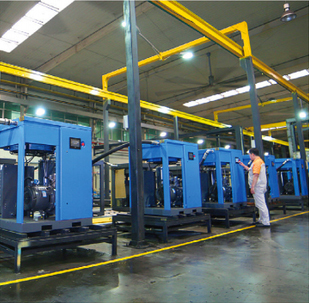
Quality Control
We practice strict quality control procedures throughout the entire production process from procuring of raw materials, processing of components, assembly of machine, to testing of machine performance.